Credit: Science Daily
Researchers have successfully incorporated washable, stretchable and breathable electronic circuits into fabric, opening up new possibilities for smart textiles and wearable electronics. The circuits were made with cheap, safe and environmentally friendly inks, and printed using conventional inkjet printing techniques.
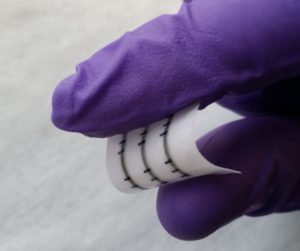
The researchers, from the University of Cambridge, working with colleagues in Italy and China, have demonstrated how graphene — a two-dimensional form of carbon — can be directly printed onto fabric to produce integrated electronic circuits which are comfortable to wear and can survive up to 20 cycles in a typical washing machine.
The new textile electronic devices are based on low-cost, sustainable and scalable inkjet printing of inks based on graphene and other two-dimensional materials, and are produced by standard processing techniques. The results are published in the journal Nature Communications.
Based on earlier work on the formulation of graphene inks for printed electronics, the team designed low-boiling point inks, which were directly printed onto polyester fabric. Additionally, they found that modifying the roughness of the fabric improved the performance of the printed devices. The versatility of this process allowed the researchers to design not only single transistors but all-printed integrated electronic circuits combining active and passive components.
Most wearable electronic devices that are currently available rely on rigid electronic components mounted on plastic, rubber or textiles. These offer limited compatibility with the skin in many circumstances, are damaged when washed and are uncomfortable to wear because they are not breathable.
“Other inks for printed electronics normally require toxic solvents and are not suitable to be worn, whereas our inks are both cheap, safe and environmentally-friendly, and can be combined to create electronic circuits by simply printing different two-dimensional materials on the fabric,” said Dr Felice Torrisi of the Cambridge Graphene Centre, the paper’s senior author.
“Digital textile printing has been around for decades to print simple colorants on textiles, but our result demonstrates for the first time that such technology can also be used to print the entire electronic integrated circuits on textiles,” said co-author Professor Roman Sordan of Politecnico di Milano. “Although we demonstrated very simple integrated circuits, our process is scalable and there are no fundamental obstacles to the technological development of wearable electronic devices both in terms of their complexity and performance.”
“The printed components are flexible, washable and require low power, essential requirements for applications in wearable electronics,” said PhD student Tian Carey, the paper’s first author.
The work opens up a number of commercial opportunities for two-dimensional material inks, ranging from personal health and well-being technology, to wearable energy harvesting and storage, military garments, wearable computing and fashion.
“Turning textile fibres into functional electronic components can open to an entirely new set of applications from healthcare and wellbeing to the Internet of Things,” said Torrisi. “Thanks to nanotechnology, in the future our clothes could incorporate these textile-based electronics, such as displays or sensors and become interactive.”
The use of graphene and other related 2D material (GRM) inks to create electronic components and devices integrated into fabrics and innovative textiles is at the centre of new technical advances in the smart textiles industry. The teams at the Cambridge Graphene Centre and Politecnico di Milano are also involved in the Graphene Flagship, an EC-funded, pan-European project dedicated to bringing graphene and GRM technologies to commercial applications.
The research was supported by grants from the Graphene Flagship, the European Research Council’s Synergy Grant, The Engineering and Physical Science Research Council, The Newton Trust, the International Research Fellowship of the National Natural Science Foundation of China and the Ministry of Science and Technology of China. The technology is being commercialised by Cambridge Enterprise, the University’s commercialisation arm.